Control Design and Improvements🔗
Control of thermal power plants is not only a matter of economic operation but also of safety. Thereby, the dynamic nature of the task, a testing and development environment is needed to develop new concepts to maximize the performance of transient process systems, including linear and non-linear model predictive controls strategies, optimal control, or AI-based controllers. Esteblishing a digital twin of the system allows to verify control concepts and parameters to reduce risky field testing, shorten commissioning times and improve reliability and performance.
Case Study on Power Plant Start-Up Optimization
Case Study on AI Based Controllers
Challenge 1: Precompile Controller Tuning to Reduce Commissioning Costs
Control systems of process plants and power plants can easily reach a complexity that is equivalent to thousands of documentation pages. During commissioning, these controllers need to be tuned to enable a stable and safe operation. However, this task can be extremely costly as it might induce contract penalties when unexpected fixes need to be implemented.
Case Study on Predictive Maintenance
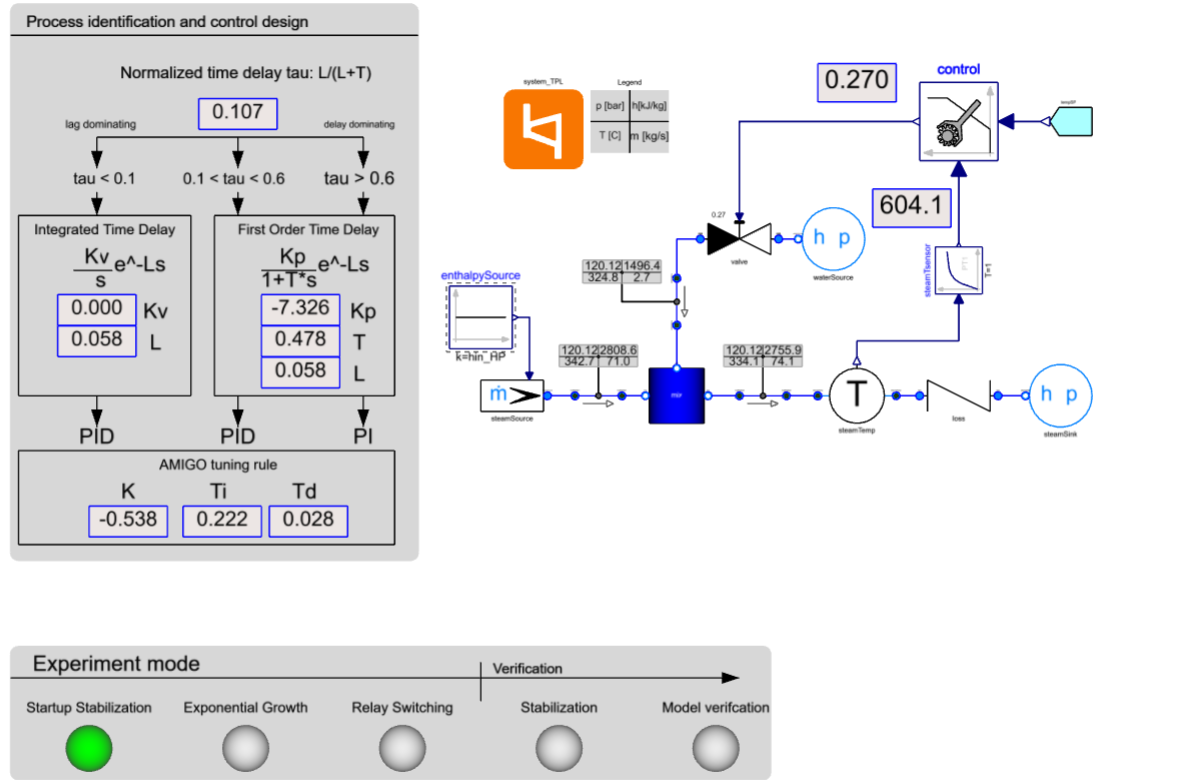
Challenge 2: Maintenance planning
Maintenance can be a large cost factor that becomes even more problematic when encountered unexpectedly. Then this can result in severe penalties due to e.g. unfullfilled heat supply to a customer. Model-predective maintenance utilizing a digital twin helps planning maintenance shut-downs.
Challenge 3: Monitoring of Critical Components
Monitoring of critical components helps is a must-have for maintenance plannning and save operation. However, some system properties cannot be measured directly at the required accuracy.
